Table of Contents
Introduction
Maintenance is the process of keeping any machine in good condition. Since everything is bound to depreciate with time, maintenance is required to preserve machine health. Predictive maintenance solutions offer a modern approach to achieving this by leveraging data to prevent failures before they occur.
Maintenance costs make up a major portion of total operating costs in most factories. Organizations spend millions of dollars on ineffective maintenance techniques. The main reason behind these extra expenses is the lack of a scheduled plan for deciding when maintenance should be performed to prevent equipment malfunctioning —predictive maintenance solutions are specifically designed to solve this.
Approaches to Maintenance
There are mainly two approaches to maintenance:
- Reactive Approach
- Proactive Approach
Reactive Approach
In the Reactive approach, we have corrective maintenance, which is nothing but running for failure management. It simply means fixing the equipment once it breaks down. This is the oldest and most expensive approach to maintenance. It means waiting for the machine to stop functioning before any maintenance activity is performed. This results in higher costs for spare parts, labor, machine downtime, and low production.
Maintenance activities performed after a jet aircraft engine has stopped working are corrective maintenance examples.
Proactive Approach
Next comes the proactive approach, which periodically performs technical assessments and inspections on the equipment and machinery to minimize the likelihood of failure. For example, performing assessments on a jet aircraft engine that is functioning properly every two weeks is an example of preventive maintenance, also known as scheduled maintenance.
Predictive Maintenance
Predictive maintenance is a condition-based preventive maintenance approach. Instead of periodically performing assessments and checks on the equipment or waiting for the equipment to fail, predictive maintenance uses actual data about the devices and equipment to predict when maintenance should be done. This approach has great economic value for the organization because it enables the proactive maintenance of machines to avoid business disruption
With the emergence of IoT, sensors can be attached to industry equipment and machinery. These sensors can monitor the equipment’s operating conditions. The information provided by these sensors can be used to analyze equipment health and calculate MTTF (mean time to failure) and RUL (Remaining useful life).
Predictive maintenance solutions leverage this sensor data to build intelligent systems that assess whether machines are operating normally mode or if there is an interruption in the workflow. These solution help schedule maintenance precisely when it’s needed, reducing unnecessary scheduled tasks and eliminating the risks of unexpected failures.
Check out BOLDConnect, an Ai IoT solution for manufacturing an that is specifically helpful in predictive maintenance.
Predictive Maintenance Approaches
Predictive maintenance can be implemented through the following techniques:
- Anomaly Detection
- Vibration Analysis
- Machine Learning
Anomaly Detection
Anomaly means something different or strange. Anomaly detection is detecting data values that deviate from the regular pattern. The idea behind this approach is simply that operational values such as temperature, pressure, and current behave in a certain way when equipment is functioning properly. An anomaly detection solution can detect values that deviate from the standard pattern and generate alerts based on that. Many algorithms are available that use different statistical techniques for anomaly detection, each with its own pros and cons.
Vibration Analysis
Vibration analysis is one of the most used techniques for predictive maintenance. The input values obtained from the machinery are analyzed concerning the Fast Fourier Transform (FFT) and Inverse Fast Fourier Transform (IFFT); based on that, a future spectrogram is obtained, which can lead to an accurate assessment of the failure of machinery or equipment.
Machine Learning
Machine learning models can be trained to predict that equipment malfunctions and requires maintenance. Furthermore, the model can be used to calculate MTTF (mean time to failure), which can be used to predict failure within a given time. In Machine learning, we have two approaches; one is supervised ML that can be used when we have enough historical data to represent all possible scenarios. The other approach is unsupervised ML, which is used when we don’t have historical data to train our model.
These approaches can be used either separately or combined to build an intelligent predictive maintenance solution that accurately predicts when equipment or machinery is likely to fail or when it needs maintenance. This can result in lower maintenance costs, higher productivity, and better product reliability.
Uncover Cost-Saving Opportunities With A Tailored Strategy
Our experts will evaluate your current maintenance processes and recommend data-driven improvements to reduce downtime and improve asset reliability.
Request a ConsultationTools for Predictive Maintenance
It requires a blend of hardware (sensors, edge devices) and predictive maintenance software (analytics platforms, AI/ML models). Below are the core tools used in building predictive maintenance solutions:
1. IoT Sensors & Gateways
- Sensors monitor temperature, vibration, pressure, humidity, and rotational speed.
- Gateways collect sensor data and transmit it to cloud platforms or on-premise servers for processing.
2. Data Lakes and Cloud Platforms
- Solutions like Microsoft Azure IoT Hub, AWS IoT, and Google Cloud IoT Core aggregate data from distributed assets.
- These platforms allow for real-time streaming, storage, and analytics.
3. Edge Computing Devices
- Devices like Azure Percept, NVIDIA Jetson, or Raspberry Pi support local processing to reduce latency and bandwidth costs.
- They enable on-site anomaly detection and real-time alerts.
4. AI/ML Platforms
- Tools such as Azure Machine Learning Studio, Databricks, and TensorFlow are commonly used to train predictive models.
- They support supervised and unsupervised learning techniques to calculate MTTF and forecast failures.
5. Data Visualization & Monitoring Dashboards
- Power BI, Tableau, or Grafana help visualize health metrics, forecast failures, and track asset performance KPIs.
- These dashboards facilitate decision-making by converting raw data into actionable insights.
Predictive Maintenance Use Cases
Predictive maintenance is industry-agnostic and drives measurable ROI across multiple sectors. Below are real-world examples:
1. Manufacturing
- Predictive models track vibration, tool wear, and spindle temperature to avoid unplanned downtime in production lines.
- This helps maintain high OEE (Overall Equipment Effectiveness) and reduces scrap rates.
2. Aerospace
- Real-time engine telemetry data is analyzed for thermal stress, vibration anomalies, and pressure fluctuations.
- Maintenance windows are optimized, reducing AOG (Aircraft on Ground) incidents.
3. Energy
- Sensors measure blade angle, torque, and generator temperature to predict component wear.
- It helps operators prevent catastrophic failures and optimize turbine output.
4. Oil & Gas
- Anomaly detection flags pressure drops, valve faults, or flow inconsistencies in pipeline systems.
- It avoids leaks, environmental risks, and regulatory violations.
5. Utilities
- Machine learning models monitor current, load, and oil temperature to identify insulation degradation.
- Enables timely intervention before grid disruptions occur.
Partner With AlphaBOLD for End-to-End Predictive Maintenance Solutions
From sensor integration to AI model deployment and dashboard visualization—we handle the complete lifecycle of your solution.
Talk to an ExpertConclusion
Predictive maintenance is no longer a futuristic concept—it’s a strategic necessity. By integrating IoT, AI, and cloud infrastructure, businesses can transition from reactive break-fix models to intelligent, data-driven maintenance practices.
- Reduced Downtime
- Optimized Maintenance Costs
- Improved Asset Lifespan
- Enhanced Operational Efficiency
At AlphaBOLD, we design and implement end-to-end predictive maintenance solutions tailored to your industry. Whether you operate in manufacturing, energy, aerospace, or logistics, we ensure your assets stay online, productive, and profitable.
Explore Recent Blog Posts
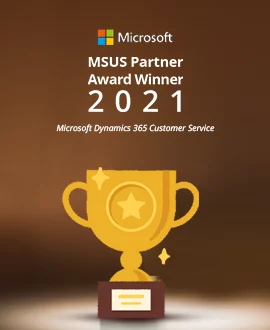